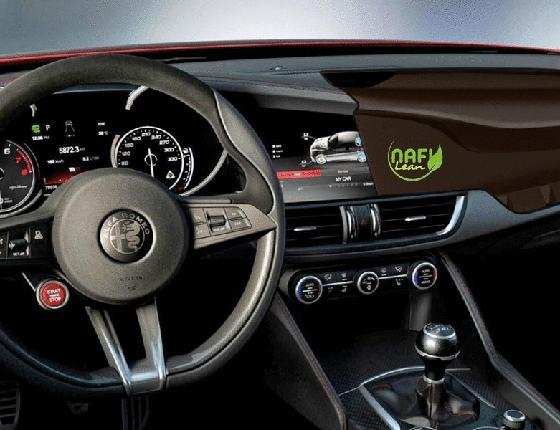
Plastic materials used in automotive industry pdfIn current years, the push for lightweight solutions and the new types of mobility that have emerged — powertrain electrification, alternative fuels, autonomous driving — have changed and are still altering the material specifications of the automotive market. For automotive applications, bio-plastics are at present restricted to interior trims and non-structural elements with ongoing analysis to boost the material properties for universal application. The mature production infrastructures of petroleum plastics, however, remain obstacles to bio-plastics becoming main stream commodity plastics. Future social pressures and subsequent market place trends and even government legislation will dictate the eventual route of bio-plastics progression.
Polycarbonate had earned the tag as the most suitable material for use in the automotive market. Nonetheless, in current instances, Polymethyl Methacrylate, the PMMA polymer or typically identified acrylic plastic, has effectively risen to the increasing demands of the automotive business in replacing polycarbonate for the most crucial use in the business, namely, automotive glazing.
The use of lightweight plastics and composite supplies in the automotive industry has been increasing in recent years due to legislative and customer demands for lighter weight, fuel effective autos. In some cases, plastics are replacing heavier ferrous materials whereas in other instances, plastics and composites are becoming added for consumer comfort purposes. In addition to being lightweight, these supplies are also tough and very easily molded. Substituting heavier materials with plastics leads to an all round weight reduction. The percent of plastics by mass in an average car has gone from six% in 1970 up to 16% in 2010 and is expected to attain 18% in 2020 2.
Challenges And Alternatives To Plastics Recycling In The Automotive Sectorplastic materials used in automotive industry pdf
plastic materials used in automotive industry pdfIn recent years, the push for lightweight options and the new forms of mobility that have emerged — powertrain electrification, alternative fuels, autonomous driving — have changed and are nevertheless changing the material needs of the automotive industry. We are also presently forging new partnerships with Kingfa and Polyram, markets leaders in the improvement of high-performance plastic components, to distribute their engineering polymers, more notably in the automotive sector. With this new solution variety, we are able to respond to a wider range of clients’ wants for homologated items, such as PA, ABS and PBT with glass fiber for side panels, technical components behind the dashboard or elements related to cabling systems.
However, pure polypropylene is sensitive to both UV rays and temperature, which can trigger it to expand. Because of the high exposure that these elements come below in the course of manufacturing and usage, several firms now print with option varieties of polypropylene. These possess a considerably much better physical and mechanical properties than common polypropylene, producing them more suited for automotive applications.
Plastics and polymer composites, which already dominate car interiors, exteriors, trim, and lighting, are gaining use in other vehicle systems as lightweight, value-producing materials that can meet increasingly challenging automotive requirements. These materials’ numerous positive aspects have enabled them to develop to turn out to be a considerable part of the components mix in the automotive sector over the past 40 years (figure three). As the push to lightweight vehicles intensifies, projections indicate that plastics and polymer composites can and should play an even a lot more substantial function in the automotive business through 2025 and beyond (figure three) 4.
A Deep Dive Into Sourcing Automotive Plasticsplastic materials used in automotive industry
plastic materials used in automotive industryIn recent years, the push for lightweight solutions and the new forms of mobility that have emerged — powertrain electrification, alternative fuels, autonomous driving — have changed and are nevertheless changing the material specifications of the automotive market. Technologically, recycling is feasible for the plastic and composite components employed in the automotive sector. Outstanding critiques of the technical aspects and possibilities for recycling plastics and composites are obtainable 1 , 15 , 16 , 26 Although recycling is virtually limited by the above mentioned obstacles, it may still be a preferred choice for these supplies and can aid to alleviate the quantity of materials being landfilled if some of the obstacles can be overcome. The feasibility of recycling can be improved by means of a handful of major avenues.
Polyurethane (PU) emerged as the second biggest solution segment in 2016. PU exhibits superior properties such as high tensile strength, abrasive strength, hardness, effect and abrasion resistance. Expanding demand from automotive OEMs and electronic appliance manufacturers for applications such as refrigeration insulation, interior trims and seat cushioning has considerably influenced the development.
An additional critical requirement for glazing is scratch resistance. Common PMMA currently has the highest surface hardness of all thermoplastics even when uncoated. However, for automotive glazing, there are stringent situations to be fulfilled to meet the ideal state of scratch resistance. The application of a coating is as a result mandatory. Contemplating that PMMA is intrinsically UV as well as weathering-resistant, a single-step coating functions nicely. In contrast, thermoplastics that have low resistance to weathering need a two-step coating method. This final results in relatively higher fees for coating.
Automotive Plastic Materials Environmental Testingplastic materials used in automotive industry
plastic materials used in automotive industry pdfIn current years, the push for lightweight solutions and the new types of mobility that have emerged — powertrain electrification, option fuels, autonomous driving — have changed and are nonetheless changing the material requirements of the automotive industry. The use of higher-strength steels (HSS), numerous versions of which are referred to as higher-strength, low-alloy (HSLA) steels in the previous decades increases drastically in the automotive sector. A single of the applications of a higher-strength, low-alloy (HSLA) steels is in Ultra-light Steel Auto Body (ULSAB) which demonstrated a 19% mass reduction in a body structure that had superior strength and structural performance (such as crashworthiness) along with a lowered parts count and net manufacturing expense savings compared to a conventional steel body. USAB, 1998 Comparable mass reductions and other benefits had been achieved for doors, hoods, decklids, and hatchbacks. Enhanced steel materials and forming processes allow a substantial optimization of automobile physique structures and components three.
The automotive composite components, reinforced plastics and polymers are among broadly preferred options for light weighting of the automobile as they offer enhanced properties such as impact strength, simple mold-potential, enhanced aesthetics, and lowered weight as compared to conventional automotive elements. The main positive aspects, which offer opportunities in the automotive market, are their prospective for maximum mass reduction of automobile and carbon emission reduction potential by light weighting of the vehicle. The elements restraining the industry are high material costs and large investments in material analysis activities by firms.
Crucial aspects restraining the automotive plastics marketplace are higher material expense and the requirement of a important investment in material research activities. At the moment, these restraints act as barriers to additional marketplace development. The utilization of new advanced supplies in automotive styles calls for new manufacturing technologies and their use in manufacturing new elements entails process re-engineering, which incurs huge capital cost.